Raja of rubber
By Lokmat English Desk | Updated: September 10, 2022 19:25 IST2022-09-10T19:25:01+5:302022-09-10T19:25:01+5:30
Yogesh Gole Srikanth Pothapragada, an engineering graduate in Electronics and Instrumentation from Anna University, Chennai worked with Accenture Consulting ...
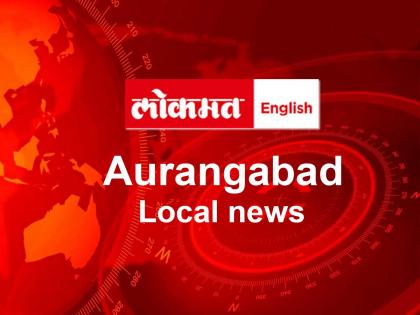
Raja of rubber
Yogesh Gole
Srikanth Pothapragada, an engineering graduate in Electronics and Instrumentation from Anna University, Chennai worked with Accenture Consulting for two years followed by a stint with a start-up Aditi Technologies. Aiming to make it big in America, the land of opportunities, he obtained H1B visa and was all set to migrate. Varroc Group MD Tarang Jain and Srikanth’s father P J Swamy, who had then formed a Joint Venture, suggested him to work with their unit which needed a competent person full-time. Srikanth, now Executive Director of Waluj MIDC-based Fores Elastomech India Pvt Ltd, decided to give it a try and stayed back. Transitioning from IT field to rubber with ease, Srikanth helped the business evolve and grow manifold.
Q: Please, tell us about your entrepreneurial journey.
A: From a JV, our company Fores Elastomech was formed when Varroc went public in 2016. We manufacture anti-vibration rubber products like bushings, mounts, hoses and technical parts for automotive and non-automotive industries. They absorb road, engine vibrations making the vehicle ride comfortable. We had begun with one customer Bajaj Auto, which even today is our major buyer. We now export 60 per cent of our products to companies in Europe and an EV startup in Vietnam. We are soon opening a plant in Chakan, Pune and a Greenfield unit in Brazil.
Q: How is your experience of working in a family-managed business?
A: I began like a professional, not as a director or president. My first post was manager, manufacturing and I worked for about three and half years on the shop floor. Handling jobs like ensuring raw material supply, planning and executing production assignments, and sending the final product to customer gave me rich experience. I then moved to engineering and even today, I head engineering. I also took care of sales and marketing and was elevated as director later. So, my journey was from bottom up. After spending five years in the business, I did MBA in marketing and finance from Indian School of Business, Hyderabad which proved very helpful.
Q: What changes and innovation you brought about in the business?
A: Traditionally, small and medium industries do repetitive work, there is little stress on research or obtaining patents. I started research in my company. We invested Rs 7 crore in the laboratory which has the state-of-the-art testing equipment. We also have software worth Rs 1 crore and can stimulate everything in-house. While working with Accenture, I realised that global companies spend 4.5 to 5 per cent of their turnover on R and D and innovation. In India, expenditure is hardly one per cent. By R and D, I don’t mean merely testing. It is something new you are developing that matters. Customer tells us, you have this much space for your product in our vehicle, you put whatever you want, I we will just put two nut bolts. So, we ourselves design and decide shape, geometry, thickness and material of our products. It’s more of material science, how you want to play around with different materials.
Rubber is a typical polluting industry. For the first time in our industry, we are working on an innovative metal treatment that is sludge-free, a zero-effluent process that does not need Effluent Treatment Plant.
Q: What is your opinion on Aurangabad as an industrial destination?
A: The city has many good engineering educational institutions. Getting skilled young people is not a big challenge here. However, Aurangabad is not able to hold skill as people are migrating for better opportunities.
Q: What changes you foresee in your field?
A: Evolution of EVs is going to be a big challenge. Currently, the engine noise conceals deficiency in bushings and mountings. In EV, there is no noise of engine so a slight variation in component can be easily perceived by customers. We are working with 12 EV platforms globally to prepare for the huge challenge ahead, focussing on aspects like alternate material, its composition and fine tuning. In internal combustion engine, engine weight was not a barrier, 200 gms here and there really did not matter. In EV, weight is very important because mileage is affected. So, exploring engineering plastic, light weighting and vibrations are the areas to think about.
Open in app